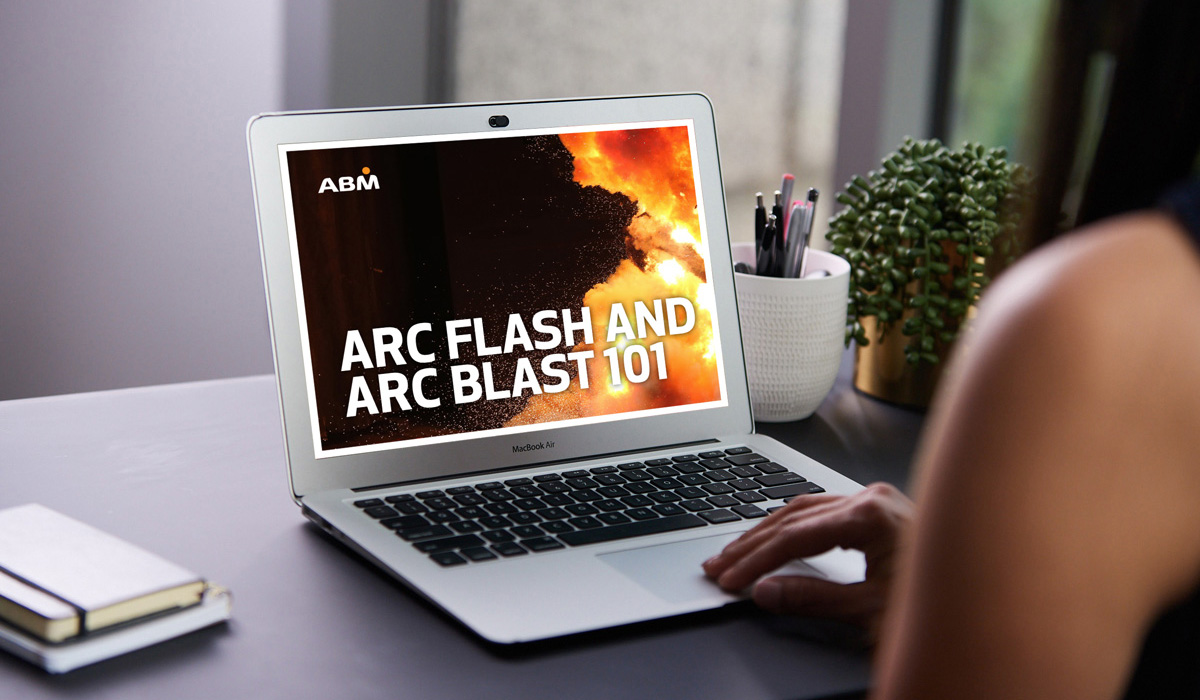
Arc Flash and Arc Blast 101
Introduction
When it comes to your electrical infrastructure, infrequent maintenance or inadequate training can lead to harmful—and even fatal—consequences. Arc flash, one of the most serious forms of electrical accidents, leads to a dangerous explosion known as an arc blast. In the U.S. alone, five to 10 blasts caused by an arc flash occur in electrical equipment every day. With an ability to produce some of the highest temperatures on earth (up to 35,000 degrees Fahrenheit, four times the temperature of the sun’s surface), an arc flash can result in devastating employee injuries and damage to your facility.
Causes of Arc Flash
- Worn or broken conductor insulation
- Exposed live parts
- Loose wire connections
- Improperly maintained switches and circuit breakers
- Obstructed disconnect panels
- Liquid near electrical equipment
- High voltage cables
- Static electricity
- Damaged equipment
- Carelessness
What’s at Stake
Total costs can range from $12 to $15 million, including medical expenses, downtime, equipment replacement, lawsuits, and insurance and litigation fees. An arc flash incident can cause current and prospective employees to view the facility as an unsafe place to work, making employee attraction and retention difficult. Potential for imprisonment up to six months and an average fine amount ranging from $250,000 to $500,000. On average, 2,000 workers are killed by an arc flash each year. Injuries can come in the form of third-degree burns, eyesight damage, hearing loss, electrocution, and disfigurement.
How to Avoid Arc Flash
- Conduct arc flash risk assessments as an OSHA safety requirement, at a minimum of every three years, to determine the amount of thermal energy that could be generated from an arc flash incident.
- Regular maintenance should follow the National Fire Protection Association (NFPA) code that states electrical equipment be maintained in accordance with manufacturers’ instructions or industry consensus standards to reduce the risk associated with failure.
- Ensure adequate electrical labeling. Arc flash hazard labels should be placed on switchboards, industrial control panels, transformers, and other central electrical equipment for maximum safety visibility.
- The correct category of PPE clothing must be approved and distributed prior to electrical maintenance. Employee training should include topics like emergency response, approach distances, and precautionary techniques.
- If energized parts are operating at more than 50 volts, it is highly recommended that equipment be de-energized if possible. De-energizing electrical equipment is the best, most reliable protection against arc flash incidents.
- Install grounding devices. High-resistance grounding devices insert an impedance into the ground return path, resulting in insufficient fault energy and a reduction in the arc flash hazard level.
For more information on safety practices, visit ABM's Electrical Power Solutions at [ABM.com/Electrical](https://www.abm.com/Electrical).