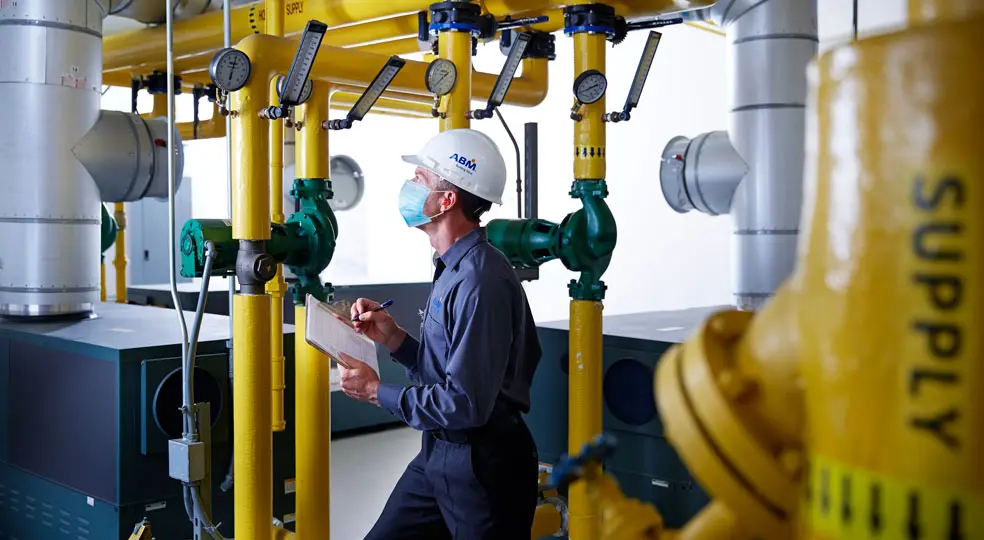
When it comes to keeping things running smoothly, there are two types of maintenance strategies: proactive and reactive.
The reactive, or “if it isn’t broken, don’t fix it,” method is common in many industrial and manufacturing companies. Facility managers often wait until equipment breaks down or problems arise, then handle repairs when they’re needed.
Proactive maintenance takes a different approach and routinely addresses facility concerns and equipment upkeep to prevent major failures. These systematic inspections identify and correct potential problems before they happen. A preventive maintenance program includes regularly scheduled tasks like cleaning, lubrication, oil changes, minor repairs and adjustments, part inspection and adjustment, or even a complete overhaul of equipment when needed.
Why Take a Preventive Approach?
A preventive maintenance program is an important part of successful facility management. It keeps equipment operating efficiently, increases the safety of your employees, and helps you avoid large and costly repairs down the road.
If you traditionally take a more reactive approach to facility management, you could be saving your company thousands of dollars by adopting a preventive maintenance program. The exact cost savings you get from preventive maintenance will depend largely on things that are specific to your company(your industry, the equipment you use, the size of your facility, and more). However, it’s generally accepted that reactive maintenance will cost you three to four times more than a preventive maintenance program.
There are multiple benefits to preventive maintenance, all of which result in better operations and saved money for your company. Here are a few examples of ways your company can benefit from a preventive maintenance program.
Reduced Downtime
Every day your facility isn’t producing at optimal levels is a loss to the company. Because you never know when equipment might fail, reactive maintenance results in unplanned downtime, which leads to idle employees, a halt in production, and missed deadlines. To get business back up and running as quickly as possible, these unexpected breakdowns will usually require paying a technician overtime and overnighting parts.
A preventive maintenance program keeps the disruption of operations to a minimum. Because maintenance checks are planned, it’s easy for you to schedule them in a way that makes the least impact on day-to-day production.In the end, you save valuable time and money by taking proper care of your equipment and keeping everything running smoothly.
Increased Equipment Efficiency and Performance
All equipment breaks down due to normal wear and tear. Using a preventive maintenance program in your facility will also keep machines in good working condition. Part replacement, fluid and oil changes, and quality inspections make sure everything works as it should. Equipment that is running efficiently uses less energy and resources than neglected machines, which, in turn, lowers your company’s power costs.
This also extends the life cycle of equipment and increases the performance of your facility. Machines break down less often, and small part replacements often reduce the need for large-scale equipment overhauls. And because the equipment you use isn’t cheap, taking better care of it lets you get more hours out of each item—leading to increased profit and decreased costs.
Safer Working Conditions
The safety of your employees is a top priority, and regular preventive maintenance can lead to improved safety and quality conditions for everyone. Routine checks uncover any hazards and prevent unsafe working conditions, so you have fewer on-the-job injuries and accidents.
Improved Company Reputation
The day-to-day cost incentives of preventive maintenance might be the biggest reason why facility managers adopt these programs, but your company’s reputation will be better off for it, too. Reactive maintenance leads to all the negative side of the things listed above—more downtime, lower equipment efficiency, and unsafe working conditions, among others. And your company’s reputation will suffer if you’re consistently putting production on hold or dealing with accident and injury cases.
Routine preventive maintenance is necessary for you to keep your company operating at its best. A reliable company that always meets deadlines and keeps employees safe will keep its customers happy, too. And a good reputation is everything.
Implementing a Preventive Maintenance Program
It will take some time and money initially to set up a program like this, but over time your company will see the benefits of regularly scheduled maintenance. If you outsource your facility services to a company with expertise in preventive maintenance, they can implement the program for you.
If you’ve previously relied on a reactive maintenance strategy and want a solution that will save you time and money and increase your employees’ safety, a preventive maintenance program is the best approach to take with your facility management.
About ABM
ABM (NYSE: ABM) is a leading provider of facility services in the United States and various international locations. ABM’s comprehensive capabilities include janitorial, electrical & lighting, energy solutions, facilities engineering, HVAC & mechanical, landscape & turf, mission critical solutions and parking, provided through stand-alone or integrated solutions. ABM provides custom facility solutions in urban, suburban and rural areas to properties of all sizes - from schools and commercial buildings to hospitals, data centers, manufacturing plants and airports.ABM Industries Incorporated, which operates through its subsidiaries, was founded in 1909. For more information, visit ABM.com.